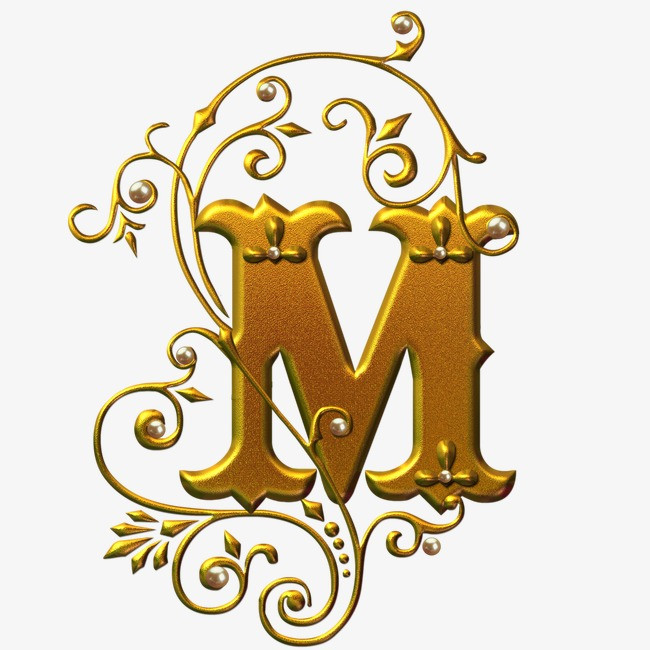
- Shandong Microwave Machinery Co.,Ltd.
- To be the Leader of microwave drying and edible oil refining equipments Manufacturer
Home> Company News> Experiment on microwave drying of wood

- AddressNo. 225, Huangqiao Village, Beiyuan, Tianqiao District, Jinan, Shandong, China
- Factory AddressNo. 225, Huangqiao Village, Beiyuan, Tianqiao District, Jinan, Shandong, China
- Phone(Working Time)+86 0531 85064681
- Phone(Nonworking Time)0086-15020017267
- Fax+ 86 0531 85064682
Experiment on microwave drying of wood
2018-10-24 17:23:41According to the sectional density distribution curves of wood specimens in the initial state before drying, during drying and under dry condition, the sectional density distribution along the thickness direction can be obtained by linear interpolation and weighted average method.
In order to eliminate the influence of micro-machining defects on wood surface and the distortion of interface measurement data, the density data of 5 scan steps (thickness about 0.5 m) in the surface layer (the first and the 21st layers) were removed when calculating the average density.
The moisture content distribution in the direction of wood thickness was the most uneven before drying. With the drying process, the moisture content in each layer of wood decreased, and the decrease extent of inner layer was greater than that of surface layer. When the moisture content is below 10%, the moisture content distribution in the whole thickness direction is very uniform.
In the process of microwave drying equipment, the moisture content distribution in each layer of wood is inhomogeneous, that is, the moisture content of wood from the surface layer to the central layer does not always increase, but fluctuates. Even when the wood is dried to a very low moisture content (the average moisture content is about 5%), the moisture content in the inner part of the wood appears. Under the condition of lower than the surface layer, but the difference of moisture content is within 0.5%, and not all the inner layers are lower than the surface layer moisture content, so it can be considered that there is no integral moisture gradient of low and high moisture content inside the whole microwave drying process, that is, there is no moisture gradient field contrary to conventional drying.
There are two reasons for the non-uniformity of moisture distribution in the drying process. One is that the distribution of microwave field intensity in wood can not be absolutely uniform during microwave drying. The other is that wood is a kind of non-homogeneous material, and the wood is caused by the non-uniform distribution of wood properties and moisture content. The dielectric properties of different parts of wood vary greatly, which makes the different parts of wood have different microwave absorption capacity. Under the combined action of these two factors, it is not surprising that there is local inhomogeneity of moisture distribution in wood during microwave drying.
However, the local inhomogeneity of moisture content distribution during microwave drying does not affect the overall judgment of moisture content distribution in wood during microwave drying, that is to say, in the whole microwave drying process, there exists a high moisture content gradient inside and a low moisture content gradient outside the wood. The results of Leiker's study were contrary to those of Leiker's, because Leiker only measured the moisture content distribution in wood after microwave drying, but did not measure the dynamic distribution of moisture content in wood before and during drying. It is not known whether the existence of the rate gradient is caused by the difference of the initial moisture content of wood or by the different drying process.
The moisture content distribution in different stages of wood microwave drying and the difference distribution of moisture content between different layers and surface layers in corresponding stages of wood drying were studied. The difference between the moisture content of the core and the surface layer is greater than that of the initial state. With the drying process proceeding, the decrease of the moisture content of the core layer is lower than that of the core layer, and the difference between the moisture content of the core layer and the surface layer is lower than that of the core layer before drying, and gradually decreases.
In the process of conventional hot air drying, the evaporation of moisture firstly occurs in the surface layer, and the moisture content of the surface layer decreases fastest, so the difference of moisture content between the inside and outside of the wood increases at the initial stage of drying. In the long period of conventional hot air drying, there are inner regions with higher moisture content than fiber saturation point (FSP) and outer regions with lower moisture content than FSP. These experimental results are in agreement with the previous hot air drying process obtained by slicing method. The variation of wood internal water content distribution is identical.
The results show that there is a gradient field of high moisture content inside and low moisture content outside the wood during microwave drying and conventional hot air drying. The difference presents a trend of first increase and then decrease.
Conclusion
In the process of microwave drying and conventional hot air drying, the moisture content in the inner layer of wood is higher than that in the surface layer, and there is a whole gradient field of high moisture content in the inner layer and low moisture content in the outer layer. In microwave drying, the difference of moisture content between inner layer and surface layer of wood decreases gradually with the extension of drying time, while in conventional hot air drying, the difference of moisture content between core layer and surface layer of wood increases first and then decreases. When the average moisture content of wood is below 10%, the moisture distribution in wood is very uniform.
High efficiency food beverage factory stone paper production line
Factory price Fully automatic Machine PP/PS Plastic Sheet Production Line
used deformered bar rolling mill production line
Manufacturing plant automatic factory puffed sticky rice cracker production line
Production Line Pp Ppr Plastic Pipe Making Machine 20-63mm Multi-layer Extrusion Production Line For Water Supply